【運営管理】工場の設備レイアウトに関する重要用語まとめ
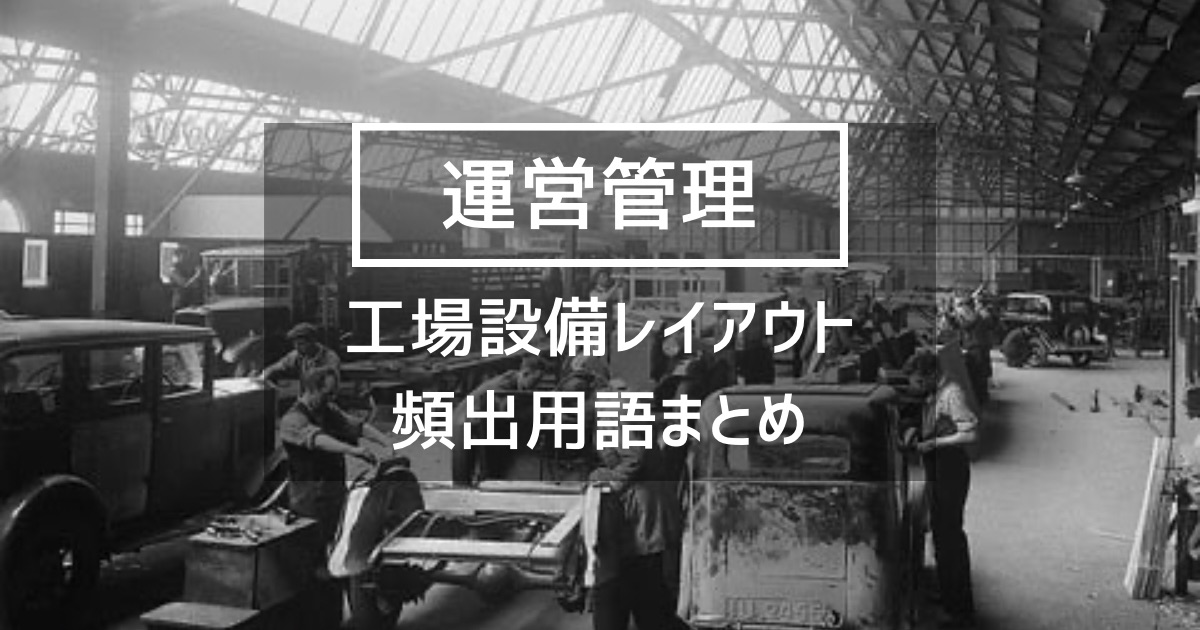
中小企業診断士試験の一次試験の運営管理に頻出の用語を知りたいと思っていませんか。
ここでは運営管理によく出題される、工場設備のレイアウトに関する用語をまとめてみました。(ここに記載した内容以外にも、出題論点はあるので参考までに。)
頻出論点の頭の整理に活用いただければと思います。
毎年、数問出題される頻出論点で、SLPは図表や手順を問われることもあります。生産形態の用語と合わせて覚えるようにしましょう。
二次試験の事例Ⅲで生産管理に関する診断・助言の出題があります。
各用語が直接問われることはないです。ただし、このへんの用語を理解した前提で事例問題が問われます。ので、一次試験でしっかり知識を貯えておく必要があります。
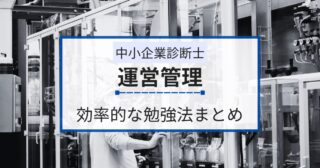
レイアウトの種類
工場設備のレイアウトの種類は大きく分けて4種類あります。
レイアウトの種類 | 特徴 |
---|---|
固定式レイアウト | 生産対象を定位置に固定したレイアウト 大型製品 |
機能別レイアウト | 同種の機械設備を1か所に集めて配置するレイアウト 小ロット生産(多品種少量生産) |
製品別レイアウト | 製品ごとに機械設備が直線的に配置されたレイアウト 大ロット生産(小品種多量生産) |
グループ別レイアウト | 製品、部品の類似性でグループ化されたレイアウト |
固定式レイアウト
生産対象を定位置に固定したレイアウト
大型製品、船舶などに適用される。
メリット | デメリット |
---|---|
設計変更に対応しやすい 大型の製品の移動を最小限にとどめることができる | 作業者や工具の移動が多くなる |
機能別レイアウト
同種の機械設備を1か所に集めて配置するレイアウト
ジョブショップ型のレイアウトで、小ロット生産に用いられる。
メリット | デメリット |
---|---|
多品種少量生産に適する 設備の稼働率をあげやすい 製品ごとにレイアウトを変えなくて良い 設計変更に対応しやすい | 製品の移動経路が複雑になる |
複数の製品を製造(ジョブ)する際に、ジョブにより作業工程と機械配置順序が異なる生産形態に対するスケジューリング
製品別レイアウト
製品ごとに機械設備が直線的に配置されたレイアウト
フローショップ型のレイアウトで、大ロット生産に用いられる。
メリット | デメリット |
---|---|
少品種多量生産に適する 作業が単純化できる 作業速度にバラツキが少なく、工程管理、進捗管理が容易 仕掛在庫が減少し、生産期間を短縮しやすい | 一部の機械の故障でライン全体が止まる 設計変更に対応し難い 熟練作業者の育成が困難 |
複数の製品を製造(ジョブ)する際に、全てのジョブで作業が類似で、作業工程と機械配置順序が同じ生産形態に対するスケジューリング
グループ別レイアウト
製品、部品の類似性でグループ化されたレイアウト
セル生産レイアウトとも呼ばれる。機能別レイアウトとの違いは、機能別レイアウトが同種の機械をグループ化するのに対し、グループ別レイアウトでは類似の機械をグループ化する点。
メリット | デメリット |
---|---|
工程間の作業のバラツキを抑えることができ、仕掛品を減らすことができる 製品の設計変更、生産量の変更に柔軟に対応可能 多能工化が可能 | 多能工の育成が必要 |
SLP
SLPとは、システマチックレイアウトプランニングのことで、工場内の適切なレイアウトと流れを計画すること
リチャード・ミューサーにより提唱された工場のレイアウト計画手法。レイアウトを構成する各アクティビティを分析し、それぞれの関連性の強さにより合理的にレイアウトを設計する手法。
SLPは以下の手順で行われる。
- P-Q分析
- 物の流れ分析
- アクティビティ相互関係図表
- アクティビティ相互関係ダイヤグラム
- レイアウト案の作成
アメリカのコンサルタント。
1961年に工場のレイアウト設計手法SLPを提唱した。著書に「工場レイアウト技術」など。
P-Q分析
何(Product:製品)をどれだけ(Quantity:生産量)生産するのかを明確にするもの
SLPにおける工場レイアウト計画で、まず最初に行うのが製品と生産量を正確に把握することである。P-Q分析では、横軸に製品の種類(Puroduct)、縦軸に生産量(Quantity)をとり、生産量の大きい順に左から並べた図を作成する。
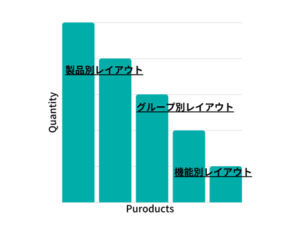
P-Q分析の結果、生産形態とレイアウトは、以下の表のように生産量の多いグループが「製品別レイアウト」、中間が「グループ別レイアウト」、少ないグループが「機能別レイアウト」とするのが一般的。をとるのが一般的である。
生産形態 | レイアウト | 物の流れ分析 |
---|---|---|
少品種多量生産 | 製品別レイアウト | 単純工程分析 |
中品種中量生産 | グループ別レイアウト | 多品種工程分析 |
多品種少量生産 | 機能別レイアウト or 固定式レイアウト | フロムツーチャート |
物の流れ分析
製品を生産する工程で、最も効率よく物が移動できる経路、順序を決める
P-Q分析の結果から、各グループに応じて、単純工程分析、多品種工程分析、フロムツーチャートによる分析をおこなう。
物の流れ分析 | 内容 |
---|---|
単純工程分析 | 加工(○)と検査(□)の2項目を表現した図表を作成し分析する。 小品種多量生産の場合、停滞や運搬が少ないため、加工と検査の2項目の分析で十分となる。 |
多品種工程分析 | 類似の製品や部品をグループ化、工程経路図を作成して分析する。 |
フロムツーチャート | 流出流入図表とも呼ばれ、生産ラインの前工程と後工程の関係を定量化し分析する |
アクティビティ相互関係図表
アクティビティの相互関係を分析するツール
生産に関わるアクティビティを近接させて配置するか、離して配置するかを評価する。アクティビティとは、建物・工場・機械・設備・倉庫・通路・出入口・採光など生産に必要な全てのもの(材料以外)。
アクティビティ相互関係ダイヤグラム
物の流れ分析とアクティビティ相互関係図表の結果をもとに、アクティビティと工程を線形に展開したもの
アクティビティ間の近接性の強さを、線の太さや線の本数で表すのが一般的。
運営管理 工場の設備レイアウトに関する重要用語まとめ
中小企業診断士1次試験の運営管理に頻出の論点として、工場の設備レイアウトについてまとめました。
ここで記載した内容は基本的な事項のみです。記載した内容以外にも出題論点はあります。
過去問や問題集を繰り返し解き、応用力を高めてください。
中小企業診断士試験【運営管理】の効率的な勉強法まとめは、別記事で詳細解説しているのでこちらも参考にしてください。
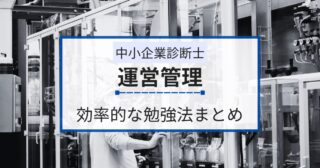
コメント